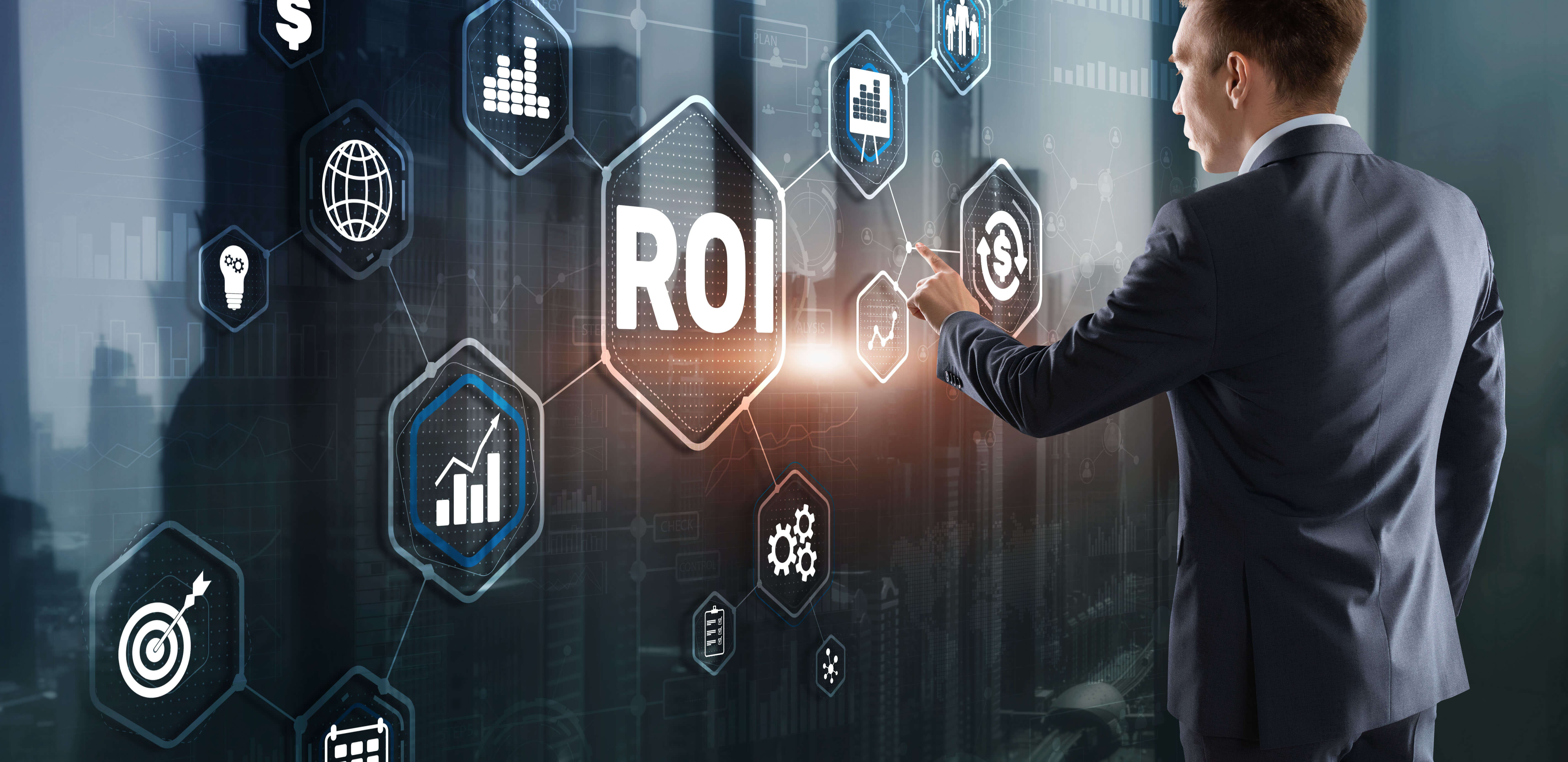
RTLS project: ROI and risk management
IoT technologies are essential for digitising production, improving efficiency and planning. Assessing costs and benefits is crucial before investing in these technologies, considering tangible and intangible returns. Risk management, through detailed analysis and pilot projects, is vital to the success of IoT projects in manufacturing.
- IoT technologies are key to the digitisation of the manufacturing process
- Carefully evaluating costs and benefits is essential for IoT investment
- Risk management is crucial for IoT project success
IoT technologies, and localisation in particular, are crucial for the digitisation of a manufacturing process, especially when it is characterised by a high movement of semi-finished products, materials and goods. Being able to create a true picture of the production progress, aligning production planning, the sales department and suppliers for the procurement of materials and parts, allows for better management of production capacity and important returns in terms of efficiency, customer satisfaction and, ultimately, profits.
As with any innovation project, once you have focused on the problem you want to solve, you need to make an assessment of the costs/benefits of the investment required and the return on investment to be made. In general, the introduction of these technologies is typically part of a process of digitisation of the production process, aimed at collecting data that over time will allow greater control of production activities and a better link with the planning and management part of the orders.
In this article we will discuss some of the main aspects that IT managers, production managers (or more generally those who have to approve the investment) must take into account in this type of evaluation. We will give some indications on the criteria with which to assess the return on investment and the aspects to take into account when assessing (and mitigating) the associated risks.
Return on Investment (ROI)
Through a return on investment analysis, an assessment is made of when the investment made in RTLS infrastructure and services will be amortised, and when the benefits will outweigh the costs.
This type of evaluation is often not easy, as measuring the economic impact of a given problem is not always possible. For example, the fact that time is lost in the search for semi-finished products is not directly related to a cost, unless it is measured and linked with the hourly cost of personnel. Similarly, the economic impact of certain events, although rare (e.g. failure to start a machine due to a missing mould), is difficult to assess.
Another aspect that makes this type of assessment difficult is the fact that these technologies can have an impact on several business functions, even if the function that initially benefits from the services offered is unique. For example, tracking forklifts in a warehouse can bring clear benefits in terms of efficiency gains in the use of this resource. However, this can also have repercussions in terms of safety in the workplace and the same tracking infrastructure can also be used to track work tools or assess the filling of certain skips in the plant.
Listed below are some criteria by which a cost-benefit analysis can be carried out. This is primarily a methodological approach, as each case is different and each company follows its own digitisation path.
Time horizon
It is important to assess the time horizon over which this assessment is made. RTLS projects, or IoT in general, have a start-up cost, which may be followed by an operational cost depending on the cost model chosen (e.g. SaaS vs. on-premise). This horizon can typically vary from a minimum of 1 to a maximum of 3 years, depending on the project to be implemented and the problem to be solved. It is however important to define this value and base subsequent evaluations on it.
Starting from known problems
The starting point for these projects is a specific need, linked to a problem that you want to solve. From here, you have to make an initial assessment of the benefits. This evaluation should, as far as possible, be based on measurable or estimable data. An example of measurable problems are:
- the time spent in the search for semi-finished products: the time lost by specialised operators in the search for parts, semi-finished products or tools can be measured over a specific time frame.
- the number of semi-finished products, or parts, lost: in a production environment (especially in the case of discrete manufacturing), it often happens that semi-finished products or parts are lost, or not found in a production time frame. This has an impact on delivery times and waste (and consequently costs).
- OEE machinery: the absence of a specific order, component or skilled operator may result in a machine not being used or remaining in operation without producing. This generally has a non-negligible cost, especially in the case of machinery with high consumption (e.g. ovens) or high value.
...
Would you like to read the full version? Fill in the form to download it for free